The Most Commonly Asked Questions in ICF Construction
Welcome to our comprehensive Q&A guide on Insulated Concrete Form (ICF) construction! If you’re considering building your dream home or looking for a sturdy, energy-efficient alternative to traditional construction methods, you’re in the right place. Below we will dive into the most asked questions about ICF construction and will try our best to update it if we start to see other questions emerge more often!
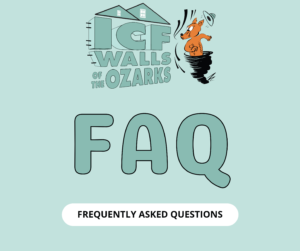
1. What is ICF construction, and how does it differ from traditional wood-built methods?
ICF construction involves using interlocking forms made of Expanded Polystyrene (EPS) foam, which are then filled with reinforcement and concrete to create a solid, durable structure. Unlike traditional wood-built methods, which rely on wooden frames, ICF construction offers superior insulation, strength, and durability.
2. What is the point of choosing to build my walls this way?
ICF walls with a 6 -inch concrete core, the block we use 99% of the time, provides a wind resistance of 250 MPH. They also provide an impact resistance of 100 MPH. Our forms have concrete core options of 4, 6, 8, 10, and 12 inch. You can customize the core size from there with EPS panels and insertable webs. With a thicker concrete core you get an increased wind resistance, providing a more durable home.
On top of the strength and safety ICF offers, this building method is proven to be up to 70% more energy efficient than other conventional building methods. Your concrete wall will have 2 continuous layers of EPS foam providing an envelope tight seal, keeping the outside temperatures where they belong. In fact, ICF is a great option if you are trying to achieve green living standards such as a passive energy home.
The other added benefits of choosing ICF are:
- Sound resistant walls. ICF walls have a STC rating of 54. Typical wood framed homes have a STC rating of 33 to 38.
- 3-hour burn rate on your walls (providing safety during wildfires and time to get to safety)
- The highest flood and earthquake rating
- Pest-resistance is provided by using termite prevention in our below grade blocks and removing your cold break with a monolithic footer and wall system.
- EPS foam is not nutritious to termites.
- Cost-effective during the building process
- Potential savings on your home insurance
3. How does the pricing of ICF construction compare to traditional wood-built methods?
While the upfront cost of ICF construction may be slightly higher than traditional methods, the long-term savings on energy bills and maintenance outweigh the initial investment. As of April 2024, we have not seen the price be more than 10% higher for the entire cost of the build. The rule of thumb in the ICF industry for an average size ICF house: you make back that difference in 4 years with the savings you see on your utility bills. Additionally, the increased durability and resilience of ICF structures can lead to lower insurance premiums over time.
4. How do you install exterior and interior applications with ICF construction?
Installing exterior and interior applications with ICF construction is straightforward. Our forms have a web placed every 8 inches. The web is the same width as a 2x4 and provides more holding power than wood when using a screw (no nails). On the form, the web is marked by the name of our manufacturer, Nudura, or a diamond pattern. You can apply your exterior/interior applications directly to our blocks, securing them to the webs. Some exterior applications will need furring strips applied to allow room for condensation, however this will still be installed directly to the webs.
The webs also act as your studs when you are hanging heavy items (i.e. your cabinets, large mirrors, TV’s, etc.). To find the web once your walls are finished:
- Use a Walabot stud finder to find these web “studs” once your wall is finished.
- Take a small finish nail and push it through your dry wall or sheet rock until you hit the web/stud.
- Go down to your trim and look for where the finish nails are placed in the trim, follow them up to find the stud.
- Once you have found 1, you can measure every 8 inches to find the next stud.
- From the corner of the room, the first stud should be 8 inches out in either direction.
5. How do you add plumbing and electrical fixtures in an ICF structure?
Adding plumbing and electrical fixtures in an ICF structure is like traditional construction methods. Electrical wiring and PVC can be installed within the foam forms after the concrete wall is poured. Any chainsaw will be able to cut channels in the foam needed for your wiring/PVC to run. Electric boxes and fixtures needing to be attached to the wall can be attached to the concrete using tap con screws. We then use a can of spray foam to cover up the cuts we have made (to avoid losing your R-value), shave it down flush with the rest of the wall once dried, and apply your sheet rock over it!
1 ½” PVC pipe will sit flush with the EPS foam when installed directly against the concrete.
6. What acts as the studs in ICF construction?
In ICF construction, the webs inside the forms act as the studs. These webs provide 3 purposes:
- They hold together the 2 pieces of EPS foam, creating the channel for the concrete.
- They provide placement for our rebar to stay in place while concrete is poured into the wall.
- They act as an attachment point for our bracing during the building/pouring process and as your stud during the rest of the building and decorating your home.
The web is made of 100% recycled polypropylene and steel and is engineered to hold a screw better than a 2×4.
7. Why would I choose ICF construction for my project?
There are numerous benefits to choosing ICF construction, including:
- Superior insulation properties, leading to energy savings and increased comfort.
- Enhanced durability and resilience against natural disasters, such as hurricanes and tornadoes.
- An increased burn rate allows your house to potentially withstand a fire and most definitely provides more time to save the most important things. Our homes have a burn rate of 3 hours, while a 2×4 has a burn rate of about 3 minutes.
- Reduced maintenance and repair costs over the lifespan of the structure.
- Excellent soundproofing qualities, creating a quieter and more peaceful living environment.
- Protection no matter what happens outside (i.e. car wrecks, attacks, etc.)
8. How does building an ICF home work with home insurance?
Sometimes people are wary of ICF because they fear that insurance companies will try and charge them more for the build type. The truth is, you should qualify for a discount due to the superiority of ICF construction. And at the very least, your home will not cost you more on insurance than a conventional method of building.
In conclusion, ICF construction offers a modern, sustainable, and cost-effective solution for building resilient, energy-efficient structures. Whether you’re constructing a new home or looking to upgrade your existing property, consider the many advantages of ICF construction for your next project. If you have any further questions or would like to explore ICF construction options, feel free to reach out to us – we’re here to help you build your dream, Legacy home!